Today, product safety and quality are more important than ever. Consumers are increasingly aware of the impact their purchasing decisions have on the environment. They are looking for products that are safe, high quality and sustainable. Therefore, companies in the process industry need to make an extra effort to ensure that their products are free from foreign bodies and contamination, especially if pumps and/or valves play an important role in their production.
Detectable gaskets have been around for years, but where are they used, how are they designed and what are their benefits? Read on to learn more about this type of technical accessory, which is often a fixture in safety and quality-conscious manufacturing companies.
Construction and application
Detectable gaskets are used to seal food and pharmaceutical processing equipment, especially pumps and valves, so that no foreign bodies end up contaminating the finished food, beverage, or pharmaceutical products. As the name suggests, they are designed to be detectable by metal detectors or X-ray equipment.
Detectable gaskets differ from other types of sanitary gaskets in that they are made from a combination of metal and rubber. One part of the detectable gasket is usually a thin strip of metal, such as iron or steel. The metal part is enclosed by rubber, which is typically made of a food and pharmaceutical approved elastomer, for example silicone or EPDM.
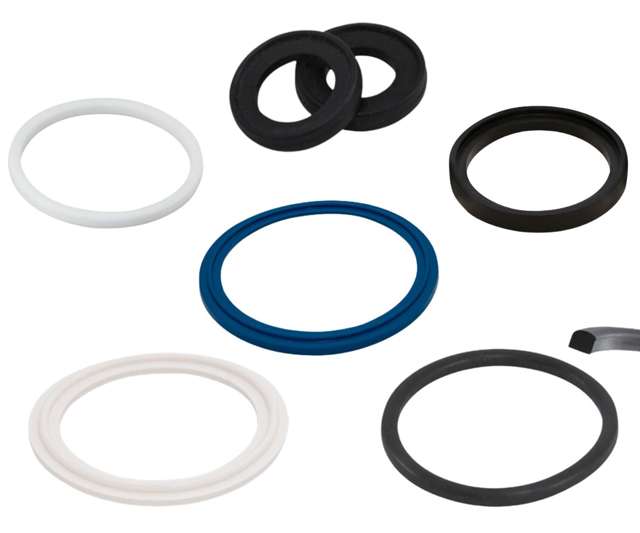
The primary benefits of detectable gaskets
Improved product safety and quality
By providing a reliable seal for food and pharmaceutical processing equipment, detectable gaskets can help prevent leaks in the process plant and resulting contamination of end products. In doing so, they also help to reduce the risk of product recalls while complying with regulatory standards and maintaining customer confidence in product safety.
Reduced maintenance costs
Detectable gaskets are durable and have a long lifetime, which can help reduce maintenance costs. By using detectable gaskets for specific production environments, it is possible to reduce the frequency of equipment downtime and maintenance.
Easy to detect
Due to their intuitive design, detectable gaskets are easy to detect with metal detectors or X-ray machines. This allows service personnel to quickly identify if a detectable gasket has failed or if there are other problems with the equipment.
Get expert help on detectable gaskets for your process plant
At Alfotech we stock detectable EPDM gaskets for dairy pipe unions for both DIN, SMS and Clamp. If you are interested in learning more about how detectable gaskets can benefit your production, please do not hesitate to contact our sales consultants who have extensive experience with this particular type of technical component. They will be able to answer all your questions and guide you to the best solution depending on your needs. Contact them now by e-mail inquiry@alfotech.eu or by phone +45 7020 0422.