Customized assembly solutions on demand
With skilled certified blacksmiths and metalworkers in our own in-house assembly workshop, we create customized assembly solutions that carefully meet your unique needs. Through our dedication and expertise, we strive to be your preferred partner in developing solutions that can improve the efficiency and quality of your production.
With us, the creative process of selecting and assembling technical components from our extensive inventory becomes an art form - a method similar to building with Lego bricks, but with a professional twist. Our goal every time is to work with you to create the most optimal solution that adds value on the production floor. We always start with the specifications you bring to the table - but we also allow ourselves to challenge them if we think we can make it even better in other ways.
Areas of expertise:
- Standard assembly
- Special assembly
- Reassembly
- Pressure testing
- Roughness measurement
- Welding
- Marking and labeling
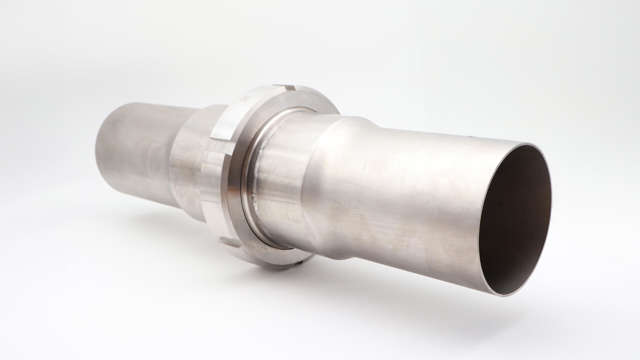
Solid welding craftsmanship
We always use the latest TIG welding technology and are certified for pipe welding in all dimensions of dairy pipes from ø6 mm and upwards.
All our welding fittings and pipes are made from austenitic acid-resistant stainless steel, also known as EN 1.4404/AISI 316L. Steel EN 1.4404/AISI 316L is the best and most commonly used steel grade in the food and pharmaceutical industries, as it is both highly corrosion resistant and very suitable for welding.
We always use formic gas as shielding gas/backing gas, as it provides the best protection of the steel's qualities and at the same time a nice visual result. The weld zone is subsequently restored by fettling unless otherwise agreed.
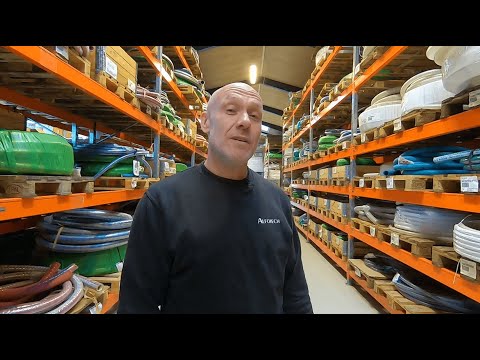
Thorough pressure testing
Pressure testing of hoses is essential to ensure they can withstand specific working pressures within the process industry. This minimizes the risk of breakdowns and leaks that can lead to serious safety and operational consequences.
At Alfotech, we ensure thorough pressure testing of the hoses before shipment, of course always according to the regulations. And of course, we will send you a pressure test certificate if you have ordered one.
Watch and listen to Peter, our Warehouse Manager, talk more about the pressure testing process and why it is so important in episode 2 of our video series Peters' Week.
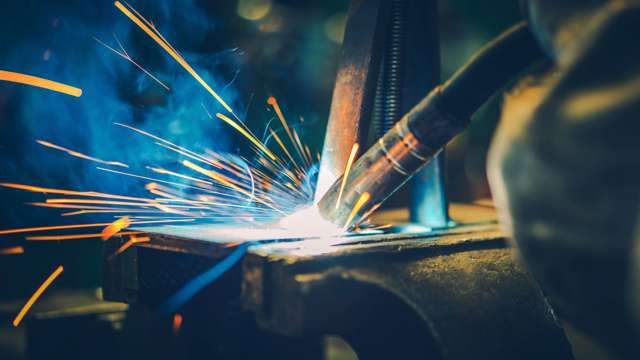
Quality assurance via WPS
As a starting point, our metalworkers work from carefully developed Welding Procedure Specifications (WPSs). WPSs act as practical “instruction manuals” that specify everything from materials and material thickness to pipe dimensions, welding parameters and back gas flow. The WPS approach ensures that welds are performed correctly and consistently, making it possible to deliver very high-quality solutions, especially for use in the pharmaceutical industry.
By following WPS, we can handle complex projects while meeting the most stringent requirements, such as ASME BPE and GMP. This is your guarantee that we deliver welding solutions that meet even the highest standards - from planning to the finished result.

Case: Bellows hoses with welding flanges
The extensive order for one of Denmark's largest OEMs included 36 specially designed bellows hoses, 18 1" and 18 2½", all equipped with 1-layer braiding according to the EN ISO 380 standard. The hose couplings consisted of hygienic welding flanges according to EN ISO 10357D requirements and included O-ring seals for optimal tightness.
Each bellows hose, which is now part of a CIP cleaning system, underwent thorough pressure testing on dispatch.
The efficiency of our team ensured delivery within just one week, demonstrating our ability to handle urgent tasks with expertise and precision.
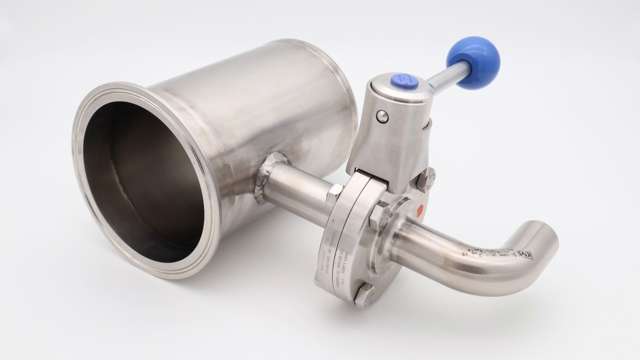
Case: Sample container with Clamp liner
A special order from a Danish manufacturer of protein powder and fat required a customized solution for their production facility. Starting with a simple picture of the old component, our assembly workshop quickly got to work on design and development. The solution included a sample container for protein production for animal feed, a 4” pipe weld with end cap, ISO Clamp liner and a standard 90° elbow. For pressure relief on disconnection, an AWH butterfly valve was fitted.
Our certified blacksmith ensured precise customization and installation in close collaboration with both our specialists and the customer to deliver the optimal solution.
Case: Butterfly valve system with sight glass
Butterfly valve system for immediate delivery to a large Danish brewery.
Butterfly valves integrated with welded T-piece and sight glass, as well as DIN nipples and nuts, all made exactly to the customer's specifications and requirements. For our blacksmith, some of the welds in this assembly were particularly challenging due to the small distances between the joints.
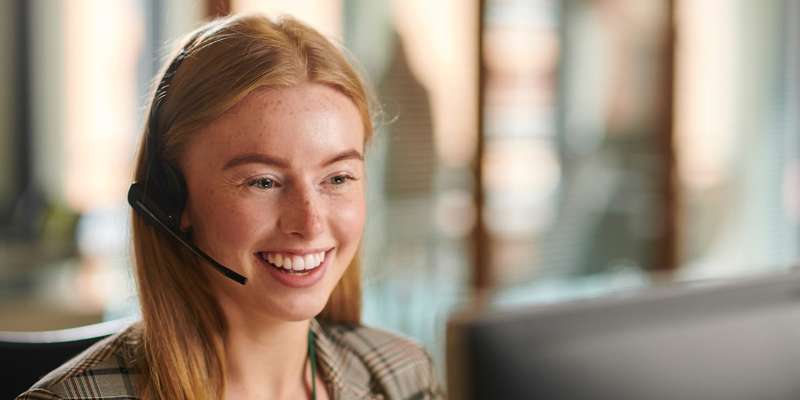
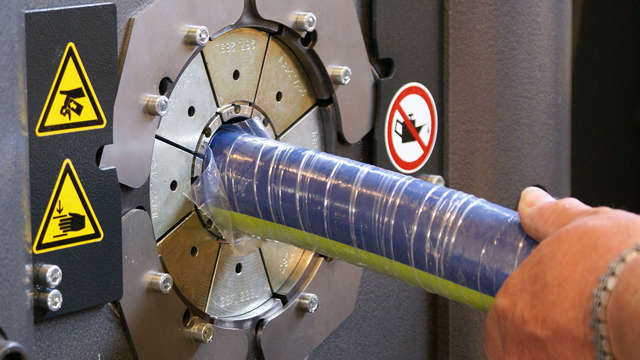
Save up to 60% via eco-friendly reassembly
With our reassembly service, you can save up to 60% on your hose solutions. So, while improving your operational economy, you reduce your environmental footprint without compromising on the quality of your equipment. That's simply common sense.
How we do it
When reassembling, we reuse the hose connectors. We first remove the hose couplings from the used hose and press the used connector onto a new hose with a new sleeve.
Documentation and certifications in order
With us, documentation and certification go hand-in-hand with the quality assurance of our installation solutions.
That is why we always ensure that what we deliver to you as a customer always meets the applicable requirements and standards in the industry in which your company operates.
The most important things to keep track of are batch numbers on hose couplings, pressure test certificates and markings.
- Batch numbers on hose couplings are critical because they enable the traceability of the hose back to its origin in the production process. This traceability is essential for identifying and addressing any manufacturing defects. Without this information, it would be almost impossible to trace a defective hose back to its origin.
- Pressure test certificate is issued after the hose has been fully assembled and pressure tested. This step is necessary to verify that the hose can withstand the pressure levels it will be exposed to in real-life conditions. The certificate serves as proof that the hose has passed this test and is safe to use.
- Marking the hoses offers an additional safety measure, as they can carry important information such as specifications, instructions for use and ownership information according to the customer's specific wishes. This ensures that the hoses are used correctly and safely in accordance with their intended purpose.