What is hard metal coating?
Hard metal coating is an innovative solution for extending the lifespan of wear parts in the process industry. This coating technique involves applying a thin, but highly robust, layer of carbide to the surface of various components. Carbide, known for its exceptional hardness and wear resistance, typically consists of tungsten carbide or titanium carbide, which is mixed with other metals such as cobalt or nickel to create an optimal balance between hardness and toughness.
In the process industry, equipment is often subjected to intense wear and tear due to constant contact with abrasive or corrosive materials. This is where carbide coating comes in as a decisive factor. It protects critical parts such as pumps, valves, and mixing equipment, significantly reducing downtime and maintenance costs. Such a coating also ensures that the equipment retains its functional integrity for longer, optimizing the production process and improving the quality of the final product.
Furthermore, hard metal coating is environmentally friendly as it extends the lifespan of components and reduces the need for frequent replacements, which reduces industrial waste. Overall, hard metal coating offers an economical and efficient solution to meet the challenges of the process industry while supporting sustainable production.
Key benefits
8x lifetime extension
Optimized production
Sustainable solution
What do you coat with?
Alfotech offers a range of advanced coating types for various industrial applications. Our coatings are made in collaboration with an experienced and ISO 9001 certified partner, ensuring high quality and reliability in all our coating processes.
Our main coatings include Chromium Carbide and Chromium Oxide, both known for their exceptional surface hardness. The Chromium Carbide coating achieves a hardness of around 1300 HV (Vickers number), while Chromium Oxide can reach up to 1500-2000 HV. This is significantly higher than untreated stainless steel, which typically has a hardness of 150-200 HV. In comparison, conventional hard chrome plating has a surface hardness of around 900-1100 HV.
In addition to these, we also offer a spectrum of other coating types, including Alumium Oxide, Tungsten Carbide, Bronze, Ni Graphite, Zr2O3, and aluminum mixed with TiO2. These alternative coatings are designed to meet specific needs and applications in different industries.
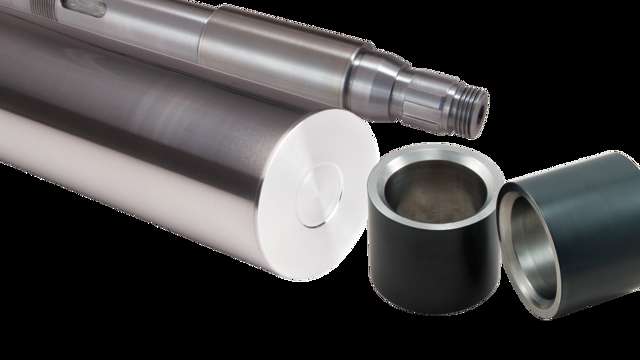
What can be hard metal coated?
Almost everything.
From new to used wear parts such as axles, axle bushings, seats and rotating parts as well as pistons and fittings.
Depending on the function of the components, Chromium Oxide, Chromium Carbide, Aluminum Oxide, Tungsten Carbide, Nigrafit and several others are used as coatings. If the wear part is in direct contact with food, FDA-approved materials are used.
Customer case: Cocio Chokolademælk A/S
Explore how Cocio Chokolademælk A/S renewed their production efficiency with Alfotech's advanced carbide coating. This technology has reduced the frequency of packaging changes and improved the lifespan of the company's equipment.
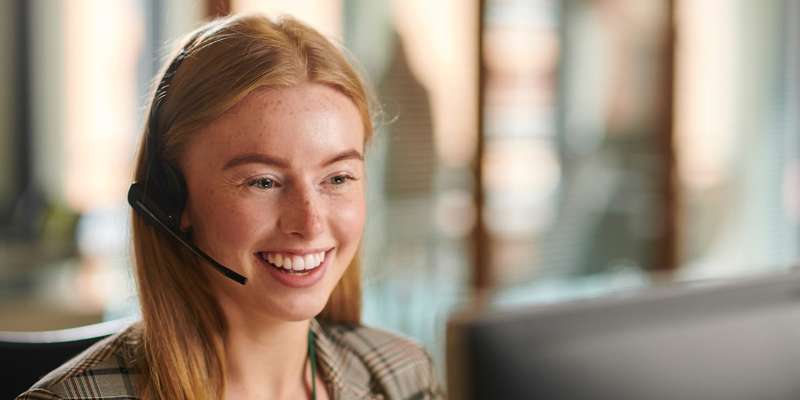