Machines in the food industry work under constant strain. Shafts, pistons and other vital parts are exposed to mechanical wear, chemicals and intensive cleaning every day. This takes a toll on components and can be costly. But wear and tear doesn't have to mean frequent replacements.
Hard metal coating (also known as carbide coating) significantly extends service life and helps reduce both costs and carbon footprint. The solution is particularly relevant in environments where high demands are placed on both chemical resistance and ease of cleaning. As highlighted in a study by Fotovvati et al (2019): "Surface protection coatings are particularly useful in applications requiring both chemical resistance and cleanability, such as medical tools and food-grade equipment."
Coating technology is an obvious choice in the food industry where hygiene and durability are crucial. It acts as an effective shield – not only against mechanical wear, but also against the detergents and acids that would otherwise gradually degrade the surface.
Example: Savings of $8.070 over 8 years
Example: Savings of $8.070 over 8 years
Imagine a shaft in a dairy. A new shaft costs, for example, $1.200 and typically lasts one year. A coated shaft costs $1.530 but lasts for eight years. The math looks like this:
- Without hard metal coating: $1.200 × 8 = $9.600
- With hard metal coating: $1.530 × 1 = $1.530
- Total savings: $8.070 over 8 years
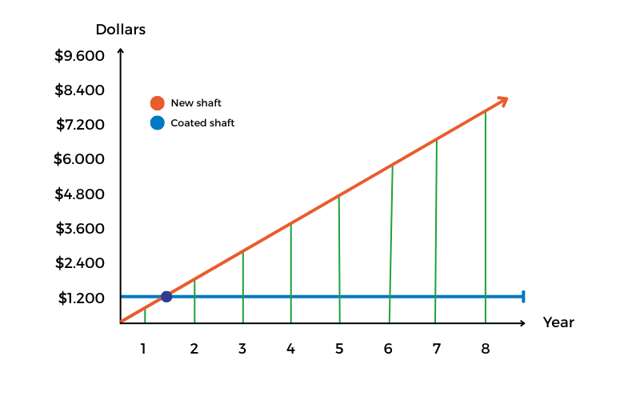
The graph above shows the difference between replacing a shaft every year and investing in a hard metal coated version that lasts for eight years. The orange line represents a new standard shaft at $1.200 per year, while the blue line shows the one-time investment in a coated shaft at $1.530. After approximately 1½ years, the two solutions are already financially equal – the so-called break-even point. From here, the coated shaft really starts to pay off. The green fields illustrate the accumulated savings year by year, which grow significantly and reach $8.070 after 8 years.
But it doesn't stop there. Beyond the spare part itself, there's even more to be gained in terms of costs associated with potential downtime, replacements, service and calibration. Each replacement requires time and thus remuneration. Machines need to be stopped, components cooled down and production adjusted. All this is avoided when the shaft lasts 8 times longer.
How it works
Hard metal coating is a surface treatment that gives components a hard, wear-resistant shell. The most commonly used coatings are chromium carbide and chromium oxide, both known for their exceptional surface hardness. They are applied by thermal spraying and effectively protect against:
- Mechanical wear and friction
- Chemical impact from acid, salt and cleaning agents
- Corrosion and microscopic cracks
Components last significantly longer, retain their form and function and require far less frequent replacement.
Valuable service solution
Many wear parts in the process industry are exposed to constant stress, such as pistons used in homogenizers in dairies.
With our hard metal coating, you get a service solution that protects components against wear and corrosion. The result? Up to eight times longer service life and fewer maintenance stops. This means lower operating costs and more stable production.
What can be coated for example?
Climate-friendly durability
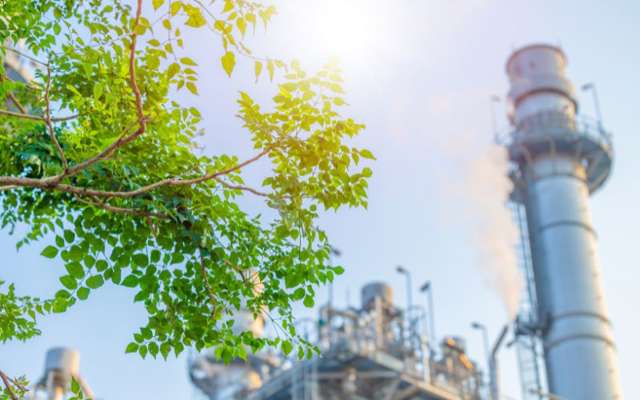
According to the German tribology organization GfT, hard metal coating can save up to 1 ton of CO₂ for every ton of raw material saved. The report "Verschleißschutz und Nachhaltigkeit" shows how coatings such as chromium carbide and chromium oxide make it possible to reuse and extend the life of components instead of producing new ones.
The fewer parts you replace, the less energy and raw materials are needed. And that makes a difference, even for small components. Getting eight times more life out of one shaft is not only good economics, it's also the climate-conscious choice.
A widespread technology
Hard metal coating is already widely used in both food and pharmaceutical production, where the requirements for hygiene, documentation and reliability are among the highest of all. The technology is thoroughly tested and documented, and the coatings are available with relevant FDA approvals so they can be used in direct contact with food without compromising safety. This makes the solution suitable for everything from shafts and pistons to pumps, valves and other components in production equipment where surface properties play a crucial role in both function and cleanability.
In addition to the significant lifetime extension, surface roughness is often reduced, making cleaning both easier and faster – and in some cases more efficient because residues and microfilm do not adhere as easily to smooth, durable surfaces.
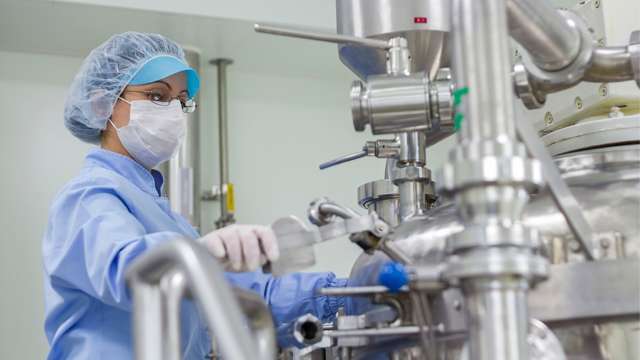
In practice, this means fewer bacteria traps and less risk of build-up in microscopic cracks and pores. For food manufacturers, this is a significant gain: The easier the equipment is to deep clean, the easier it is to comply with traceability, documented cleaning and microbiological control requirements.
At the same time, wear and tear from cleaning agents and frequent washing is reduced, so components are not degraded by the maintenance itself. This means longer uptime and better conditions for keeping equipment in top shape, even in productions with high demands for cleanliness and frequent changes.
In a nutshell: Hard metal coating is not just a solution to wear and tear. It's also a reinforcement of cleaning routines and an important support for the food safety on which the entire process depends.
The importance of surface for hygiene and durability
When a component wears out, it's rarely the whole part that fails. It’s typically the surface that loses its smoothness and becomes more difficult to clean. In food production, where hygiene requirements are often high, smooth and easy-to-clean surfaces are crucial. A rough or degraded surface can collect residue, provide good growth conditions for bacteria and complicate daily cleaning.
Instead of replacing the entire shaft or piston, the surface can be renewed. The component is cleaned, restored and prepared to meet hygiene and food safety requirements again. This makes it possible to reuse the existing parts without compromising on function or safety.
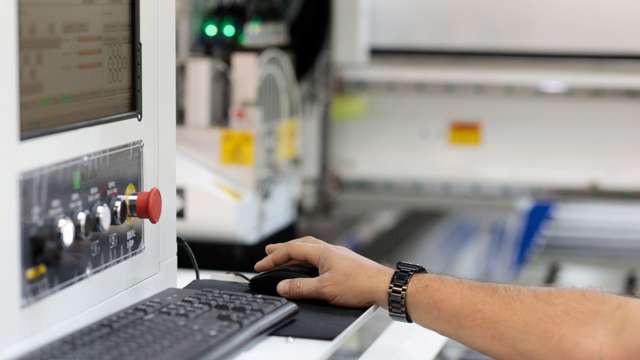
For example, imagine a shaft that has been in operation for three years under daily cleaning and changing loads. The surface is showing signs of wear and tear – not in the form of deep damage, but as fine cracks and unevenness that interferes with cleaning. The core is still solid and with a new hard metal coating, the component can be brought back to full function. The new surface is smooth, durable and resistant to both chemicals and moisture.
When wear and tear no longer requires a full replacement, but just a surface treatment, a much more flexible maintenance strategy is achieved. Planned stops become planned stops – not urgent solutions. This creates better management of both spare parts and resources and makes it easier to document maintenance to the quality department. In short: Keeping the surface in top shape not only strengthens cleaning routines, but also overall reliability.
Operational benefits and long-term value
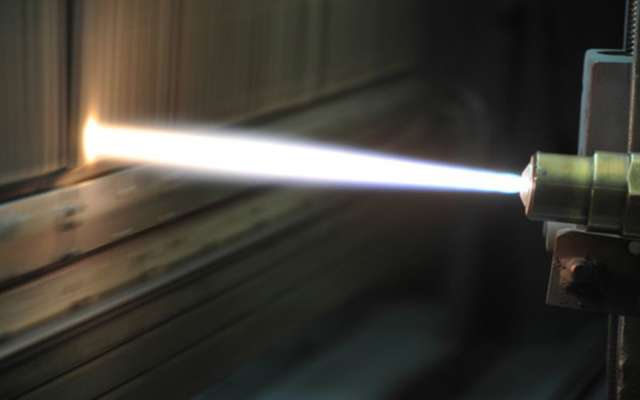
Hard metal coating may not be the cheapest solution in the short term, but it’s among the most sensible when you consider operation, durability and resource consumption over time. A coated component can last up to eight times longer than a standard solution. This means fewer replacements, less downtime and more stable production with fewer unexpected interruptions.
It also saves time and resources that would otherwise be spent on ordering, transporting and assembling new parts. When components last longer, capacity is freed up for other tasks –and production can concentrate on what creates value. As GfT puts it: "If you use products longer, you save resources of all kinds." It's not just about materials, but also about better use of time, energy and facilities.