In the process industry, many unsung heroes exist among the technical components used daily in manufacturing companies. Components that ensure that processes remain both efficient and hygienic, while often providing operational benefits.
One of the most popular of these heroes is the flange coupling, which is especially prevalent in food and pharmaceutical production - and for good reasons!
In the following, we focus on what the flange coupling is, where it’s used, and its main benefits as an integral part of the process plant. Perhaps you've wondered if the flange coupling could help optimize your production processes?
Read on and be better equipped to make the right choice!
What is a flange coupling and how does it work?
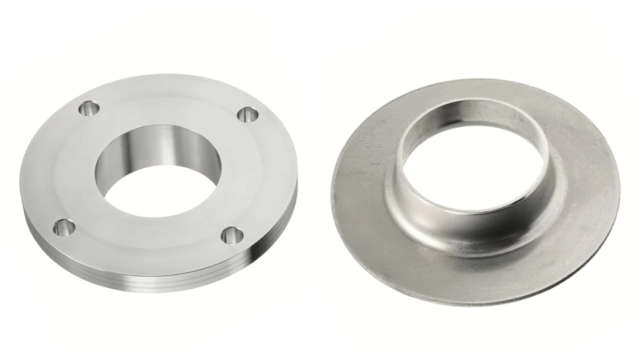
As an assembly, the flange coupling consists of the flange itself, which is often available with 4 or 8 holes depending on the dimension, and an associated liner (weld on) adapted to the flange hole. The loose flange is characterized by its ability to rotate independently of the liner around the central axis of the hose. The fixed flange, on the other hand, cannot rotate because both the flange and liner are molded in one piece. Common to both types is the stainless-steel construction, that they’re bolted to the remaining pipe system and always installed with a gasket or O-ring.
Whether it's a loose flange or a fixed flange, our assembly workshop always welds the flange coupling to the hose connection piece itself, which is pressed onto the hose. Such hose assemblies can of course also be designed with 45- or 90-degree bends along with rotations in 45-degree intervals as needed.
3 good reasons to consider the flange coupling
In the process industry, the flange coupling often plays a crucial role in ensuring that the production line operates safely and efficiently. It often contributes significantly to maintaining high standards of hygiene and quality, especially in the production of food and medicine where precision and hygiene are paramount.
Here are some of the key benefits of the flange coupling:
- Flexible installation: Easy to mount and dismount, making it easy to replace or adjust components in the production line, saving time. This makes it ideal for process plants where changes or adjustments are made regularly.
- Hygienic design: The low surface roughness combined with a compatible gasket or O-ring ensures a tight connection, prevents bacteria build-up and facilitates easy cleaning. This not only reduces the risk of contamination, but also ensures longer equipment lifetime and less maintenance.
- Robust construction: Withstands both high pressures and temperatures and can handle the toughest production conditions without compromising on performance, for example during CIP or SIP cleaning. The high quality significantly increases reliability and reduces downtime.
Did you see our YouTube video about the aseptic loose flange? In the video, we not only show a concrete example of one of our innovative hose solutions developed in our in-house assembly workshop, but we also highlight the main benefits of the aseptic loose flange in food and pharmaceutical production.
The important choice: regular vs. aseptic flange coupling

The flange coupling is often a crucial technical component in the process industry as it ensures a tight and stable connection in the process plant. The choice between a regular and an aseptic flange coupling depends on your specific requirements for tightness, hygiene and durability in relation to the production environment. The difference between these two types lies primarily in their design standards and application areas.
- Regular flange coupling: Suitable for production environments with less stringent hygiene criteria, and where resistance to pressure and chemical influences is in focus. Typically follows standards such as DIN and ANSI/ASME, which specify dimensions, material requirements and pressure classes without taking aseptic needs into account. Ideal for water, oil and gas production, and chemical industries where robustness and cost-efficiency are paramount. Although it has some surface roughness, this is acceptable when hygiene is not the primary goal.
- Aseptic flange coupling: The way forward if you have strict hygiene requirements. Often used in the food, pharmaceutical and biotechnology industries where sterility is essential to avoid contamination. The aseptic flange coupling follows DIN, ISO and ASME BPE connection standards, which ensure smooth surfaces without dead zones, helping to minimize bacterial growth. They often require materials that can withstand repeated sterilization, and the design makes it possible to achieve a tight and hygienic seal without large gaskets.
When choosing a flange coupling, it's important to consider both economy and application requirements. A regular flange coupling may seem like a budget-friendly choice while also being robust. However, it’s not suitable for sterile environments. Conversely, the aseptic flange coupling costs slightly more and requires more maintenance, but it meets the strictest hygiene requirements needed in aseptic production environments.
Think carefully - so you get the best out of your investment!
Configure with loose flanges in the hose configurator
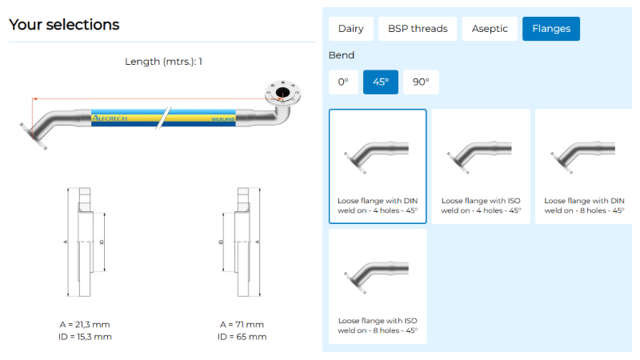
With our updated hose configurator, you can customize your very own hose solution in less than 2 minutes, complete with loose flanges! Once you’ve selected your desired hose and its dimensions, you can easily add loose flanges according to DIN/ISO connection standards, along with any necessary bends and rotations. You always have a clear overview of your hose configuration in the "Your choices" section on the right side of the screen. It doesn't get any easier than that!
If you’re unsure which flange coupling is best suited for your production, our experienced sales consultants are always ready to discuss how you can achieve the most optimal and efficient solution. Contact us now by phone +45 7020 0422 or email inquiry@alfoteh.eu.